Understanding and Maximizing Pressure Die Casting Tools
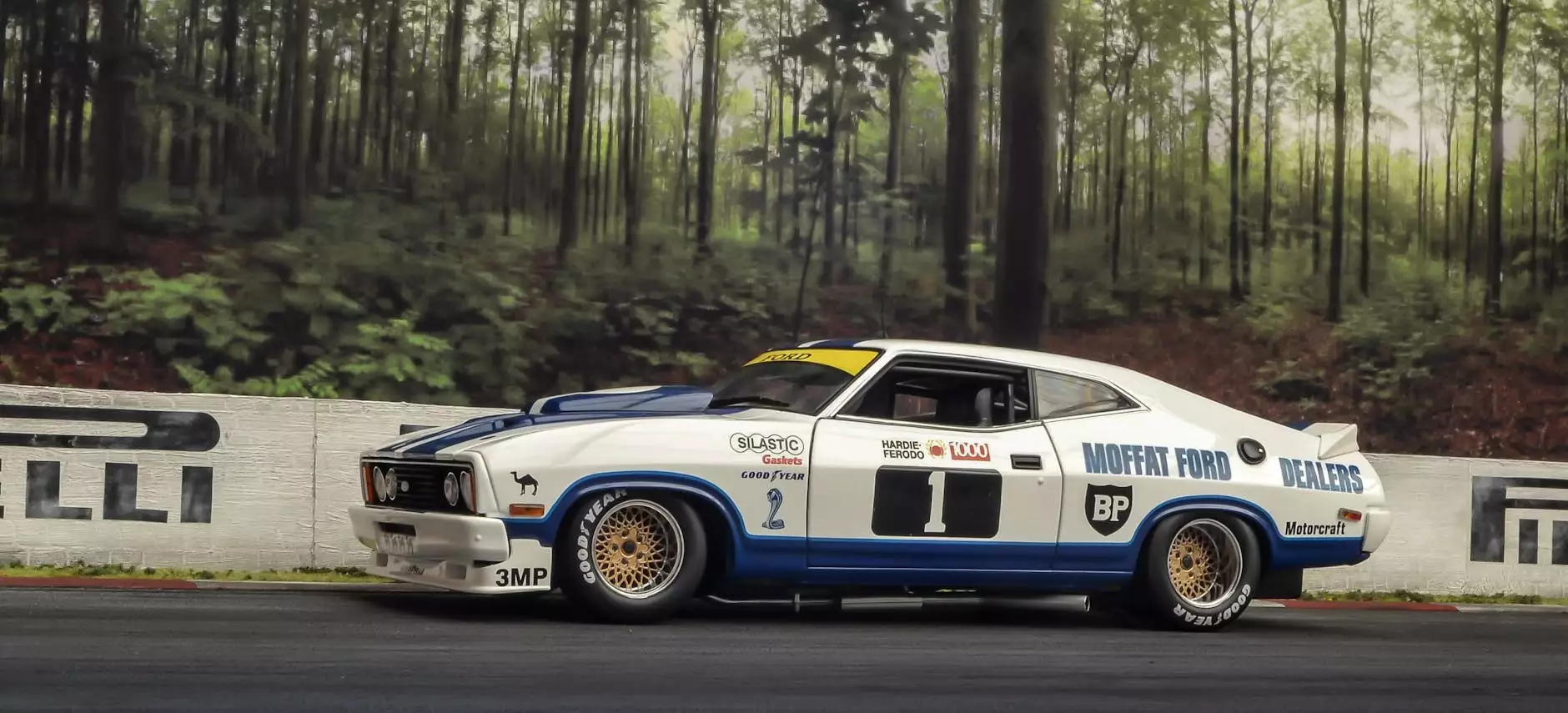
Introduction to Pressure Die Casting Tools
Pressure die casting tools are essential components in the automotive, aerospace, and consumer goods industries. These tools enable manufacturers to create complex and detailed metal parts with high precision. This article will delve into the intricacies of pressure die casting tools, their importance, applications, and the benefits they bring to the metal fabrication sector.
The Basics of Pressure Die Casting
Pressure die casting is a widely used manufacturing process that involves forcing molten metal into a mold cavity under pressure. This method ensures that the molten metal fills the mold completely, resulting in parts with excellent surface finishes and tight tolerances.
Key Components of Die Casting Tools
The effectiveness of pressure die casting largely depends on the quality and design of the casting tools involved. The key components include:
- Molds: Custom-designed molds dictate the shape and finish of the final product.
- Injection System: This component is responsible for injecting molten metal into the mold at high pressure.
- Ejector System: Post-casting, this system helps in removing the finished product from the mold without causing damage.
- Cooling System: Efficient cooling ensures that the molten metal solidifies uniformly, preventing defects.
- Heating Elements: In some sophisticated systems, heating elements are used to maintain the temperature of the molten metal during injection.
The Advantages of Using Pressure Die Casting Tools
Utilizing high-quality pressure die casting tools offers a multitude of benefits for manufacturers, such as:
- High Production Rates: The rapid cycle time of the die casting process leads to increased production rates.
- Precision & Quality: Tools designed for precision ensure that the final products conform to exact specifications with minimal tolerance variations.
- Cost-Effectiveness: While the initial investment in die casting tools may be substantial, the long-term cost savings associated with reduced material waste and increased efficiency are significant.
- Versatility: Pressure die casting tools can be utilized for various metals, including aluminum, zinc, and magnesium, catering to a wide range of applications.
- Reduced Need for Finishing: The smooth surfaces produced by die casting often require little to no finishing, saving time and resources.
Applications of Pressure Die Casting Tools
Pressure die casting tools are employed across numerous sectors, demonstrating their versatility and capability. Some of the key applications include:
Automotive Industry
The automotive industry relies heavily on pressure die casting for manufacturing components such as:
- Engine blocks
- Transmission housings
- Wheels
- Structural components
Aerospace Sector
In aerospace, weight reduction without compromising strength is critical. Pressure die casting facilitates the production of lightweight parts that meet stringent safety and performance standards. Typical applications include:
- Aircraft frames
- Brackets and supports
- Engine components
Consumer Products
Pressure die casting is also common in the manufacturing of consumer products. Examples include:
- Kitchen utensils
- Decorative hardware
- Appliance shells
Challenges in Pressure Die Casting
Despite its numerous advantages, pressure die casting does come with certain challenges that manufacturers must understand and address:
Tool Wear and Damage
The high pressure and temperature involved in the process can lead to rapid tool wear. Regular maintenance and employing high-quality materials for tool construction can alleviate these issues.
Complexity of Design
While die casting allows for intricate designs, the complexity can also pose challenges in terms of mold design and manufacturing. Collaborating with skilled engineers is vital for optimizing designs for manufacturability.
Metal Shrinkage
As metals cool, they shrink, which can sometimes lead to defects in the final product. Proper mold design and cooling techniques are essential to manage this phenomenon effectively.
Choosing the Right Pressure Die Casting Tools
To maximize the benefits of pressure die casting, it is crucial to select the right tools. Here are some considerations:
- Material Selection: Choose materials for the molds that can withstand high temperatures and pressures.
- Mold Design: Ensure that the mold design accommodates the thermal expansion of the metal to minimize defects.
- Supplier Expertise: Partnering with experienced suppliers can significantly impact the quality and efficiency of the die casting process.
The Future of Pressure Die Casting Tools
As technological advancements continue to evolve, the pressure die casting industry is poised for transformation. Innovations such as additive manufacturing, advanced simulation software, and AI-driven predictive maintenance are set to change how pressure die casting tools are designed and utilized.
Embracing Automation
Automation in the die casting process can lead to improved consistency and efficiency. Robotic systems can accurately handle parts, reducing human error and enhancing safety.
Sustainability Practices
The pursuit of sustainability is increasingly influencing manufacturing processes. Implementing energy-efficient practices, recycling materials, and reducing waste are becoming integral parts of the pressure die casting process.
Conclusion
In summary, pressure die casting tools are a cornerstone of modern metal fabrication, driving innovation and efficiency across various industries. Their ability to produce high-quality components at scale makes them indispensable in manufacturing processes. Embracing the latest advancements in technology and maintaining high standards in tool design and maintenance will enable businesses to fully leverage the advantages of pressure die casting. As the industry evolves, staying informed and adaptive will be key to maintaining a competitive edge in this dynamic field.
For more information and expertise on pressure die casting tools, consider reaching out to professionals at DeepMould.net, your trusted partner in metal fabrication and casting solutions.