How to Mold ABS Plastic: A Comprehensive Guide
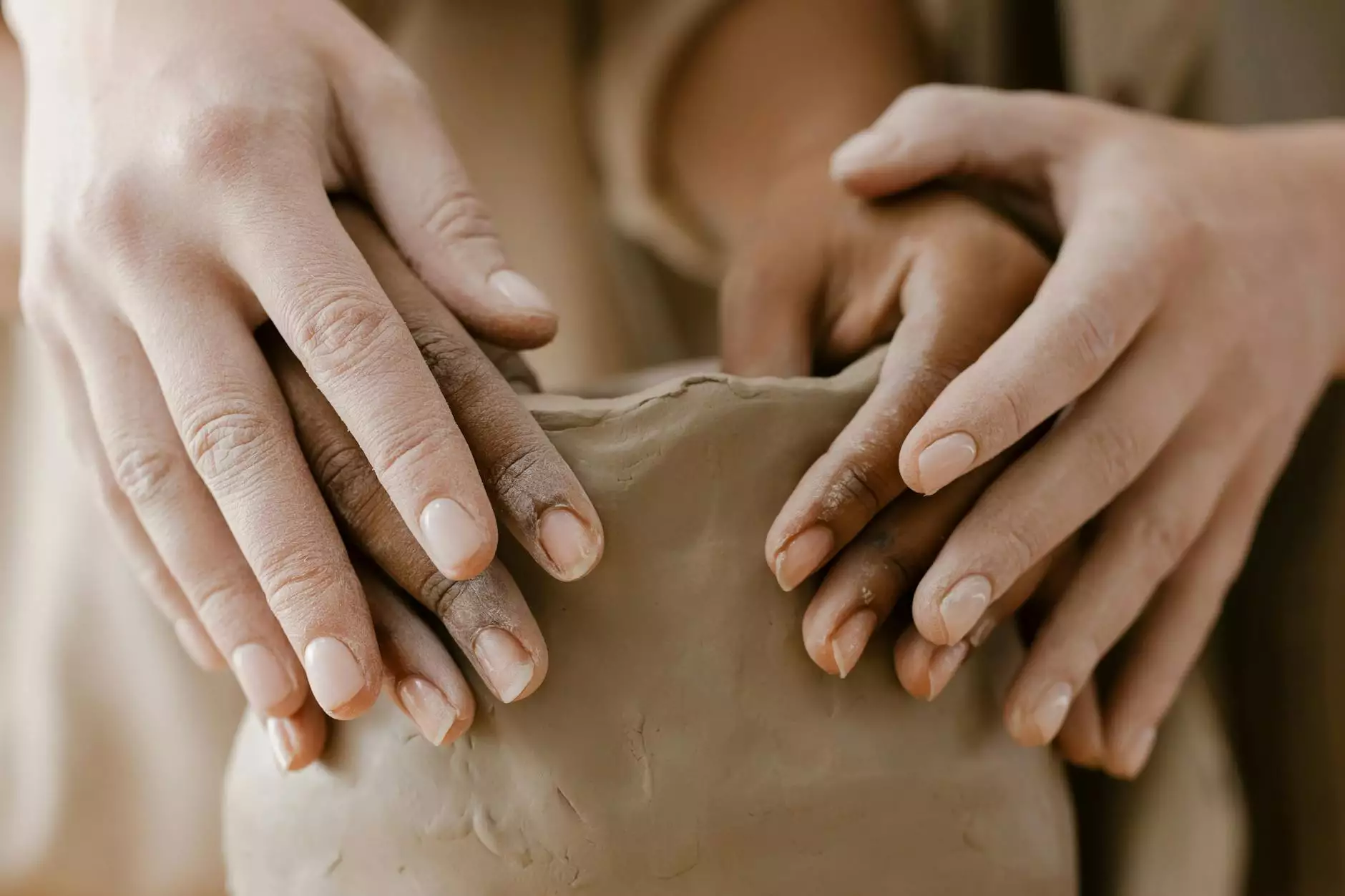
ABS plastic, known for its durability and versatility, is a favorite among manufacturers and hobbyists alike. Understanding how to mold ABS plastic effectively is crucial for achieving high-quality products. In this article, we will explore the entire process, from preparation to final product, ensuring you have all the information you need to succeed in your projects.
What is ABS Plastic?
Acrylonitrile Butadiene Styrene (ABS) is a thermoplastic polymer known for its excellent impact resistance and toughness. It is popular in various applications, including consumer goods, automotive parts, and electronic housings. The material's favorable properties make it an ideal choice for molding processes.
Why Choose ABS Plastic for Molding?
- Durability: ABS is highly resistant to impact and physical stress, making it suitable for demanding applications.
- Lightweight: Compared to metals, ABS is significantly lighter, reducing overall product weight.
- Cost-Effectiveness: ABS is less expensive than many alternatives, making it a budget-friendly option.
- Good Machinability: ABS can be easily machined, heated, and reshaped, providing flexibility in design.
- Aesthetic Appeal: ABS can be finished to achieve a smooth surface for a polished look.
Essential Equipment for Molding ABS Plastic
To effectively mold ABS plastic, you will need the following equipment:
- Injection Molding Machine: This machine melts and injects the ABS material into the mold cavity.
- Molds: Custom-designed molds are crucial for forming the desired shape of the product.
- Heating Element: A reliable heating system ensures that the ABS is melted to the correct temperature.
- Cooling System: Proper cooling mechanisms help solidify the ABS quickly, reducing cycles times.
- Quality Control Instruments: Tools for measuring dimensions and quality assurance throughout production.
Steps for Molding ABS Plastic
1. Design the Mold
Creating an effective mold is the first step in the molding process. The mold should be designed considering the final product's dimensions, features, and functionality. CAD (Computer-Aided Design) software can be extremely helpful in visualizing and planning the mold design.
2. Prepare the ABS Material
Before molding, prepare the ABS material by:
- Drying: ABS should be dried to remove moisture that can lead to defects in the product.
- Coloring: If coloring is required, add colorants to the ABS resin before processing.
3. Set Up the Injection Molding Machine
Configure the injection molding machine with the correct temperature settings. ABS typically requires a temperature of around 230°C to 260°C for melting. Ensure that heating elements and cooling systems are working properly to achieve optimal results.
4. Inject the ABS into the Mold
Once everything is set up, the ABS is injected into the mold under high pressure. The speed and pressure of injection can significantly affect the quality of the molded part.
5. Cooling Phase
After the ABS has been injected into the mold, it’s important to allow sufficient cooling time to solidify the material. Cooling should be uniform to prevent warping and internal stresses within the part.
6. Ejecting the Part
Once the cooling phase is complete, eject the molded part from the mold gently. Taking care during this process will help maintain the integrity of both the part and the mold itself.
7. Post-Processing
After ejection, consider any required post-processing. This can include:
- Trimming: Remove excess material or sprues.
- Painting: Apply paint for aesthetic purposes.
- Surface Treatment: Add coatings or finishes for enhanced durability.
Common Challenges in ABS Molding and Solutions
1. Warping
Warping can occur if the cooling process is too rapid or uneven. To mitigate this, ensure consistent cooling rates and adjust mold temperatures as needed.
2. Surface Defects
Surface defects such as blemishes, bubbles, or sink marks can arise from improper processing. Maintain optimal molding temperatures and pressures and ensure the mold surfaces are smooth and well-maintained.
3. Dimensional Accuracy
If parts do not meet the required dimensions, check your mold design and injection settings. Fine-tuning these factors can help achieve better dimensional accuracy.
Conclusion
Understanding how to mold ABS plastic can open up a world of possibilities in product design and manufacturing. By following the steps outlined above and ensuring that you are well-equipped with the right tools and knowledge, you can create high-quality ABS parts that meet your needs. Whether you are a manufacturer or a hobbyist, mastering the molding process will enhance your capability to produce reliable and durable products. For top-quality molds and expert advice, consider partnering with professionals like Hanking Mould, a leading plastic mold maker and plastic injection mould manufacturer.
Get Started with Hanking Mould
Are you ready to dive into the world of ABS plastic molding? Reach out to Hanking Mould today. Our team of experts is here to assist you with the best molds and advice needed to bring your projects to life!